Suspension bridge technology is one of the oldest and most widely used technologies. The reason for this is that it is the product of a very simple idea: when encountering an obstacle, overcoming it by hanging a rope of sufficient strength between the two sides of the obstacle. Although materials and forms may change, the main idea remains the same.

For example, the Incas would turn the grasses near the location where the bridge was to be built into fibers, and then use these fibers to create ropes for constructing suspension bridges. Since the lifespan of this material is at most one year, this process must be repeated annually. People would gather on a day declared as the “bridge construction festival” and collectively produce fibers and ropes. As they weave these fibers from both sides of the bridge and meet in the middle, a great festive joy is celebrated. During this time, the old bridge is sent off with a final gesture of respect, merging into the river’s waters. Since the Incas also performed arithmetic operations and stored numerical information by tying knots on these fibers, the bridge they built is a kind of walkable abacus.
As the world of physics advanced to the quantum level, it was inevitable that bridges would also evolve.
Stress ribbon bridges, while based on the same simple idea as other suspension bridges, are far more complex and advanced structures compared to the bridges of the Incas. Despite their simple and minimalist appearance, they require much more precise and detailed analysis and design than many other types of bridges.
The system, invented by the German structural engineer Ulrich Finsterwalder, was first proposed in 1953 for the Bosphorus Bridge.
In the stress ribbon bridge system, the main load-bearing elements consist of high-strength cables.
For a 30-meter span with a uniform distributed load of 3 tons per meter, a steel beam with a height of 1 meter is required to carry the load. The self-weight of this beam is approximately 8 tons. The same load can be carried by a steel cable with a diameter of only 50 millimeters and a self-weight of half a ton. The steel cables used in modern bridges can withstand 6-8 times more tension compared to structural steel profiles. However, as the cables sag under this load, they also apply intense horizontal forces to the connection points at the edges. For this reason, stress ribbon bridges are generally built today for pedestrian use.
Precast reinforced concrete elements are typically used as the deck. The thickness of these elements does not exceed 500 millimeters at their thickest point. After being stored for a period to reduce shrinkage effects, the precast concrete elements are suspended from the main load-bearing cables and pulled into place along the cables.
To protect the main load-bearing cables and post-tensioning cables within the deck, seal the joints between deck elements, and achieve a smooth deck surface, cast-in-place concrete is applied.
In the final stage, the precast elements are compressed using post-tensioning cables to prevent tensile stresses in the reinforced concrete elements under all loading conditions.
With the increased mass of the concrete deck, the bridge is much less affected by dynamic loads such as pedestrian and wind loads.
Without the need for intermediate piers or scaffolding for assembly, wide spans can be crossed quickly and with minimal materials.
For the design of stress ribbon bridges, staged construction analyses are performed. It is crucial to account for time-dependent material behavior in reinforced concrete.
The stiffness of the steel load-bearing cables changes at each stage depending on the load they carry, exhibiting nonlinear behavior. Ambient temperature also significantly affects the stresses in the cables.
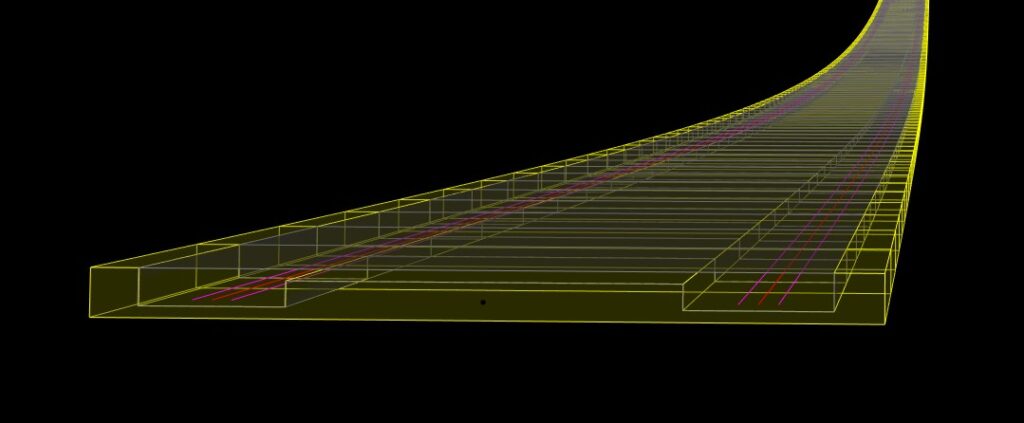